Especialistas en el control de sólidos
-
Ingeniería de procesos
-
Programación SCADA
-
Armarios eléctricos
-
Instalaciones eléctricas
-
Programación PLC´s y HMI´s
-
SAT presencial y a distancia
-
Proyectos de gestión y Big Data
SOLUCIONES
Medición en continuo llenado de silos | Microdosificadores | Transporte neumático | Retrofit instalaciones obsoletas | Granulación productos pulverulentos | Molienda vía seca | Sistema Control de producción (ICS) | Secado de arcillas | Cribado o Tamizado de arcillas | Filtrado aire-medioambiente | Dosificación materias primas | Dosificación por batch o BIG BAG | Dosificación por depeso | Dosificación por cinta transportadora |
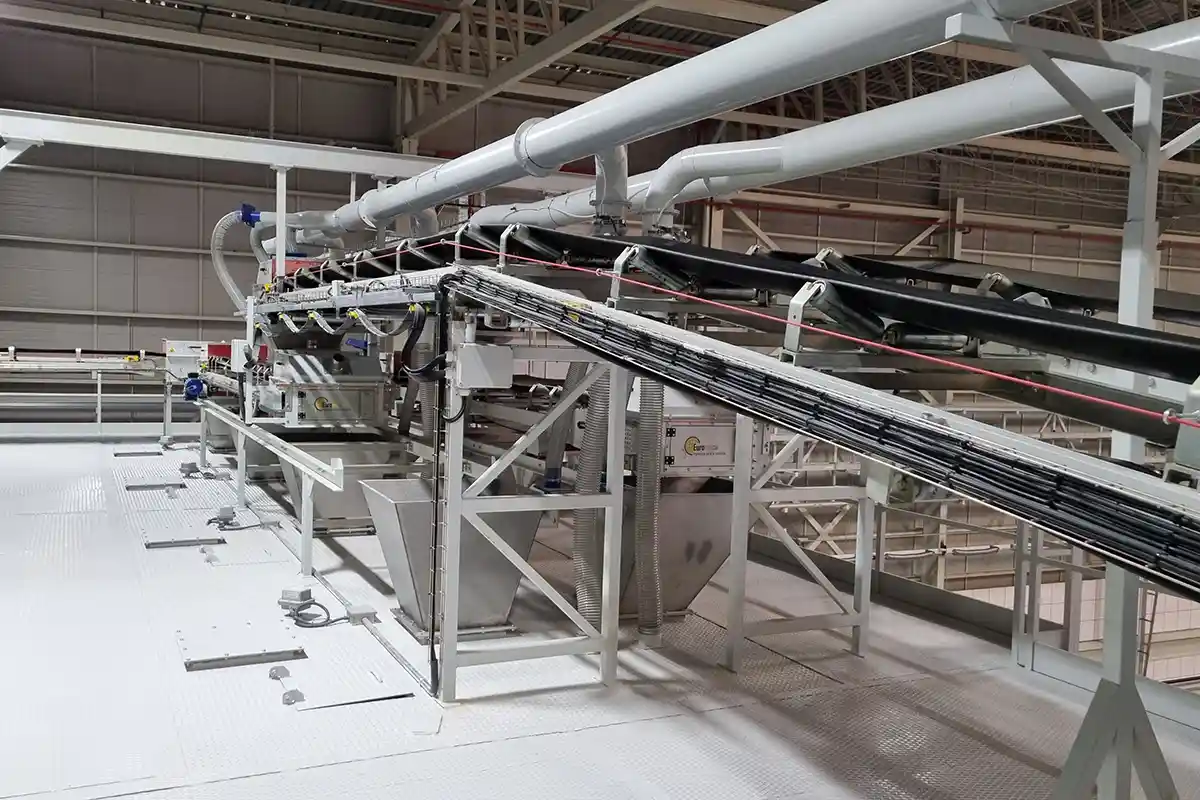
Medición en continuo llenado de silos
La medición en continuo del llenado de silos es un proceso importante en muchos entornos industriales donde se almacena y maneja materiales a granel. Hay varias técnicas de medición disponibles, cada una con sus propias ventajas y desventajas.
Una técnica comúnmente utilizada es la medición de nivel mediante sensores ultrasónicos o de radar. Estos sensores emiten una señal y miden el tiempo que tarda en rebotar en la superficie del material almacenado para determinar la distancia entre el sensor y la superficie del material. A partir de esta medición, se puede calcular el volumen del material y estimar el nivel de llenado del silo.
Otra técnica utilizada es la medición de presión diferencial. Se instalan dos sensores de presión en diferentes alturas dentro del silo, y se mide la diferencia de presión entre los sensores para determinar la altura del material y, por lo tanto, el nivel de llenado del silo.
También se pueden utilizar sensores de peso para medir el peso del silo y el material almacenado. A partir de la diferencia de peso, se puede calcular el nivel de llenado del silo.
Para el sector cerámico, se utilizan técnicas de medición similares a las mencionadas anteriormente. La elección de la técnica de medición dependerá de factores como el tipo de material cerámico almacenado, la forma del silo y el entorno de trabajo
Microdosificadores
Son dispositivos que permiten dosificar de manera precisa y exacta pequeñas cantidades de materiales en el proceso de producción industrial. Estos dispositivos utilizan la dosificación gravimétrica y/o volumétrica, lo que asegura una alta precisión en la dosificación de los materiales.
Además, están formulados para el coloreado en continuo de los productos industriales, lo que permite obtener un acabado homogéneo y de alta calidad en el producto final.
Los microdosificadores tienen una resolución de pesaje de al menos +-1 gramo, lo que garantiza la exactitud en la dosificación de los materiales. Esto es especialmente importante en la producción industrial, donde la precisión en la dosificación es fundamental para asegurar la calidad del producto final.
Por último, estos microdosificadores son muy aconsejables para evitar la manipulación de microaditivos peligrosos. Al automatizar el proceso de dosificación, se reduce el riesgo de exposición a materiales peligrosos y se mejora la seguridad en la producción industrial.
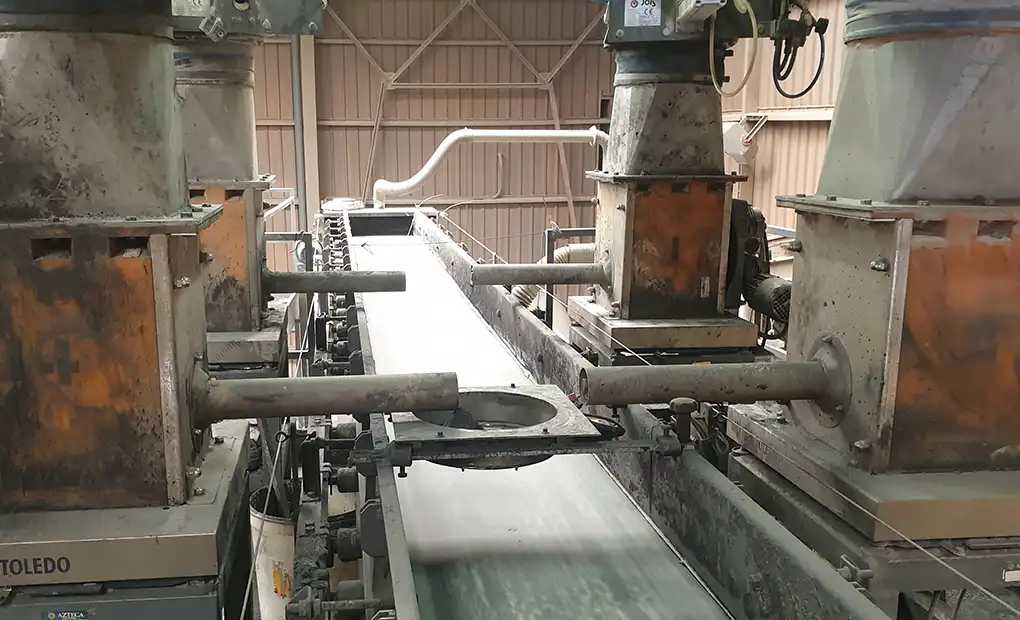
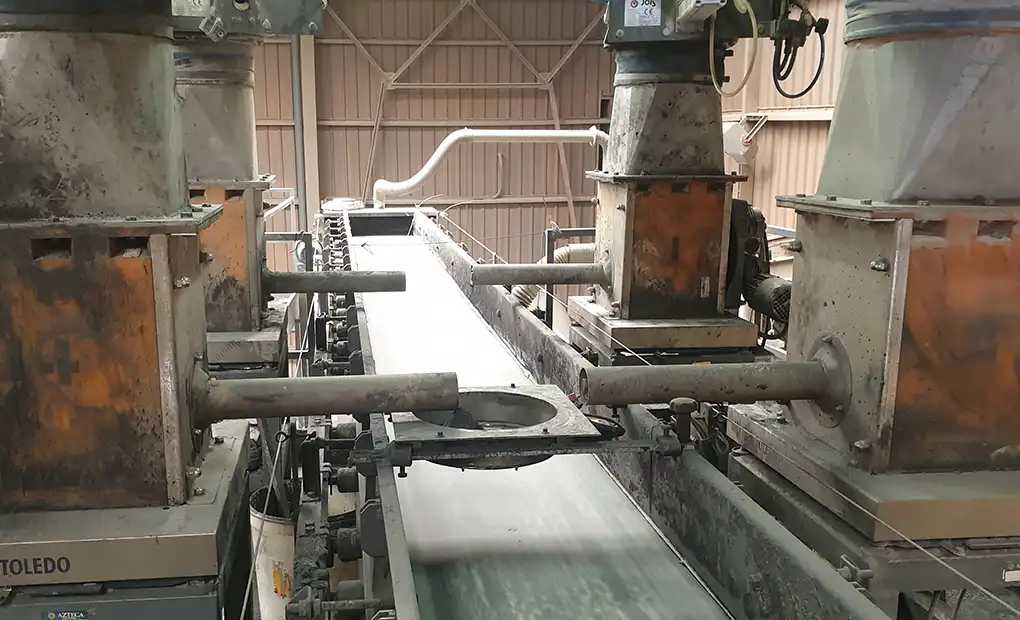
Microdosificadores
Son dispositivos que permiten dosificar de manera precisa y exacta pequeñas cantidades de materiales en el proceso de producción industrial. Estos dispositivos utilizan la dosificación gravimétrica y/o volumétrica, lo que asegura una alta precisión en la dosificación de los materiales.
Además, están formulados para el coloreado en continuo de los productos industriales, lo que permite obtener un acabado homogéneo y de alta calidad en el producto final.
Los microdosificadores tienen una resolución de pesaje de al menos +-1 gramo, lo que garantiza la exactitud en la dosificación de los materiales. Esto es especialmente importante en la producción industrial, donde la precisión en la dosificación es fundamental para asegurar la calidad del producto final.
Por último, estos microdosificadores son muy aconsejables para evitar la manipulación de microaditivos peligrosos. Al automatizar el proceso de dosificación, se reduce el riesgo de exposición a materiales peligrosos y se mejora la seguridad en la producción industrial.
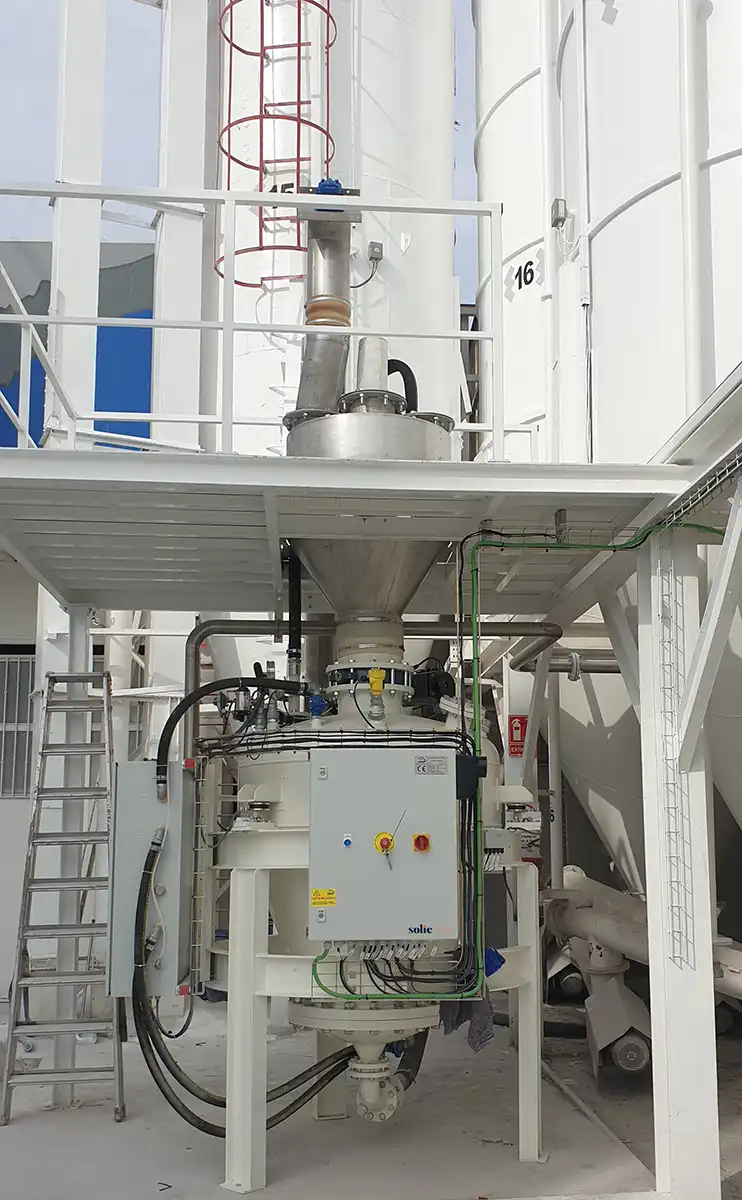
Transporte neumático
Se trata de un proceso para el transporte de material sólido o pulverulento desde un punto a otro por medio de un flujo de aire a presión, ya sea positiva o negativamente, y a través de una tubería. Según el tipo de material a transportar (abrasividad, granulometría,etc) existen varias variantes, transporte en fase densa por paquetes, fase densa fluidificada, fase diluida, por aspiración.
fase fluida. La principal ventaja respecto a otros elementos son, el menor espacio que ocupan y la ausencia de polvo en el entorno.
Retrofit instalaciones obsoletas
El retrofit de instalaciones obsoletas es un proceso en el que se actualiza y moderniza una instalación existente para mejorar su rendimiento y funcionalidad.
Somos especialistas en retrofit de instalaciones de pesaje.
El proceso de retrofit puede ser una solución muy rentable ya que permite aprovechar la estructura mecánica existente de la instalación, evitando así el costo de una nueva construcción y minimizando el tiempo de inactividad.
Además, los especialistas en retrofit de instalaciones de pesaje ofrecen costes muy sorprendentes y tiempos de cambio especialmente cortos, lo que permite a las empresas obtener mejoras significativas en la calidad y producción de sus productos en un plazo relativamente corto.
Otra ventaja importante del retrofit es la incorporación a la industria 4.0, que permite una mayor automatización y digitalización de los procesos de pesaje y control de calidad, lo que mejora la eficiencia y la productividad de la instalación.
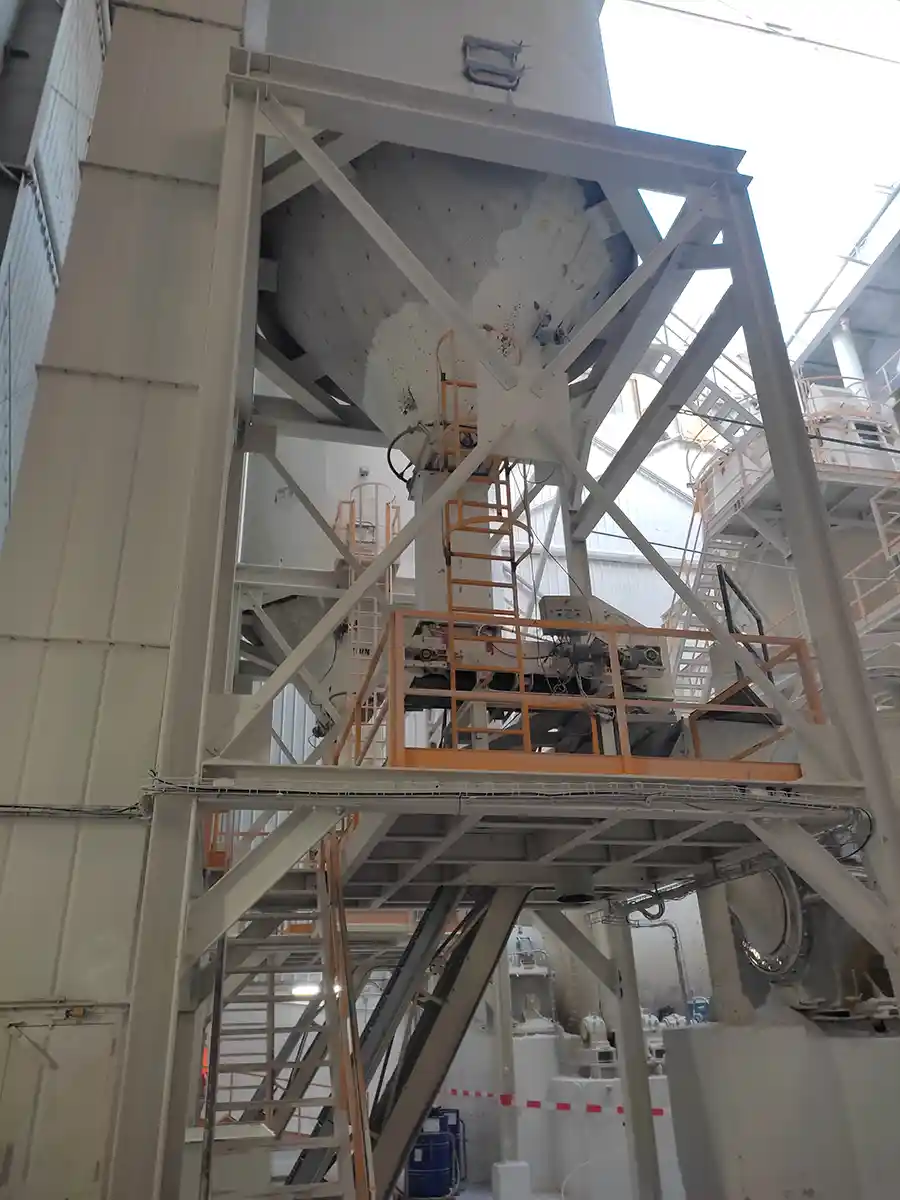
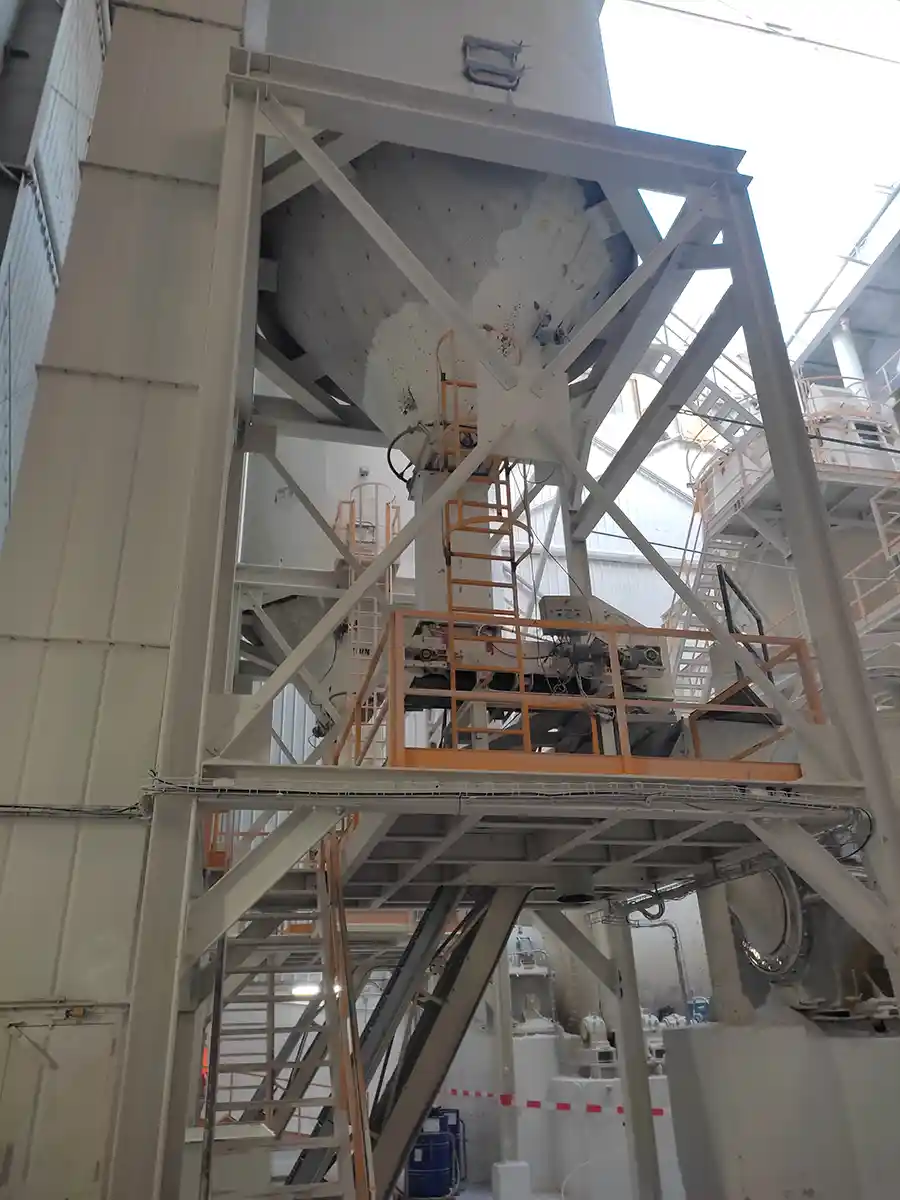
Retrofit instalaciones obsoletas
El retrofit de instalaciones obsoletas es un proceso en el que se actualiza y moderniza una instalación existente para mejorar su rendimiento y funcionalidad.
Somos especialistas en retrofit de instalaciones de pesaje.
El proceso de retrofit puede ser una solución muy rentable ya que permite aprovechar la estructura mecánica existente de la instalación, evitando así el costo de una nueva construcción y minimizando el tiempo de inactividad.
Además, los especialistas en retrofit de instalaciones de pesaje ofrecen costes muy sorprendentes y tiempos de cambio especialmente cortos, lo que permite a las empresas obtener mejoras significativas en la calidad y producción de sus productos en un plazo relativamente corto.
Otra ventaja importante del retrofit es la incorporación a la industria 4.0, que permite una mayor automatización y digitalización de los procesos de pesaje y control de calidad, lo que mejora la eficiencia y la productividad de la instalación.
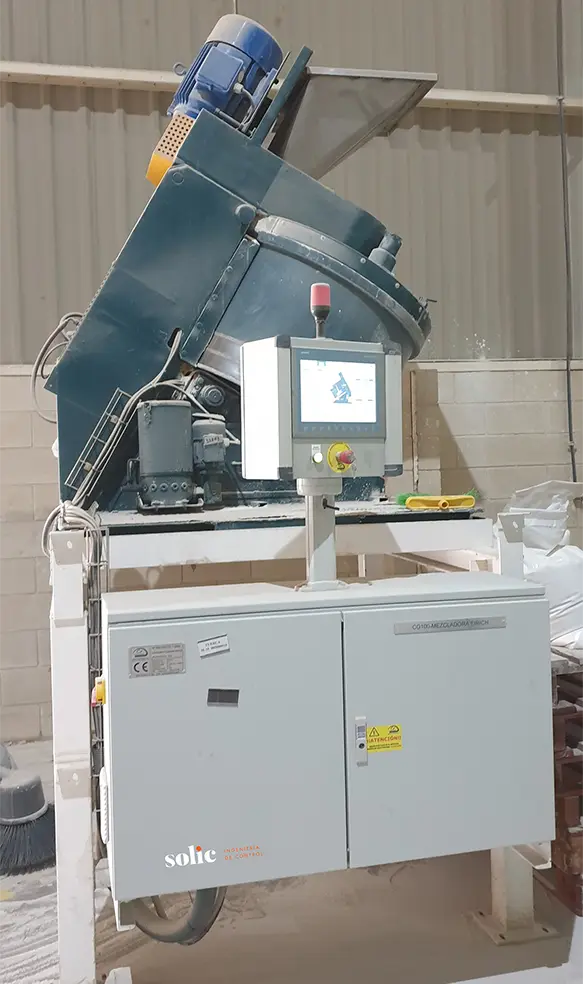
Granulación productos pulverulentos
Es un proceso utilizado en la industria para transformar polvos en granulados. Este proceso consiste en agregar un líquido (generalmente agua) al polvo, lo que permite formar pequeñas partículas o gránulos.
También, puede ser un proceso importante en la producción de diversos productos, ya que permite mejorar su manejo, transporte, almacenamiento y aplicación. Los gránulos son más fáciles de dosificar y mezclar, y su forma es más estable y menos propensa a la segregación que los polvos.
En la industria, se utilizan diferentes técnicas para la granulación de productos pulverulentos, como la granulación por vía húmeda, la granulación por vía seca y la granulación por vía fundida. Cada técnica tiene sus ventajas y desventajas, y se selecciona según las características de los materiales a granular y las especificaciones del producto final.
Molienda vía seca
Es un proceso utilizado en la industria para reducir el tamaño de partícula de materiales sólidos sin utilizar ningún tipo de líquido. En este proceso, los materiales sólidos se trituran y pulverizan mediante la acción mecánica de molinos, como molinos de bolas, molinos de martillos, molinos de rodillos, entre otros.
Su utilización en la industria es frecuente, debido a que es un proceso eficiente y económico para reducir el tamaño de partícula de una amplia variedad de materiales, como minerales, productos químicos, alimentos, entre otros.
El material se alimenta al molino y se tritura mediante la acción de impacto, corte y fricción entre las partículas y las superficies del molino. El material molido se recoge en un recipiente o silo, donde se puede almacenar para su posterior uso o procesamiento.
Este proceso tiene algunas ventajas en comparación con la molienda vía húmeda, como la menor necesidad de secado y la menor cantidad de residuos líquidos generados. Sin embargo, la molienda vía seca puede generar una mayor cantidad de polvo, lo que puede requerir medidas de seguridad adicionales para prevenir la exposición de los trabajadores a sustancias peligrosas.
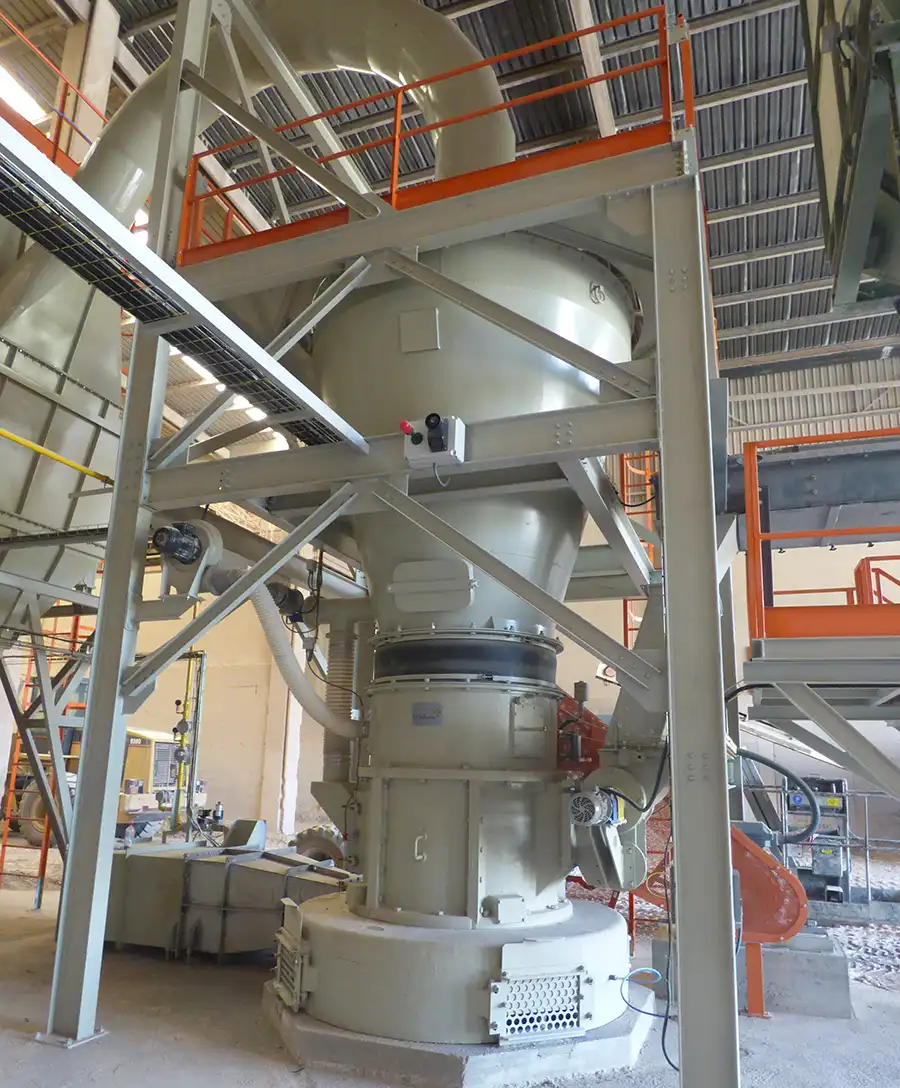
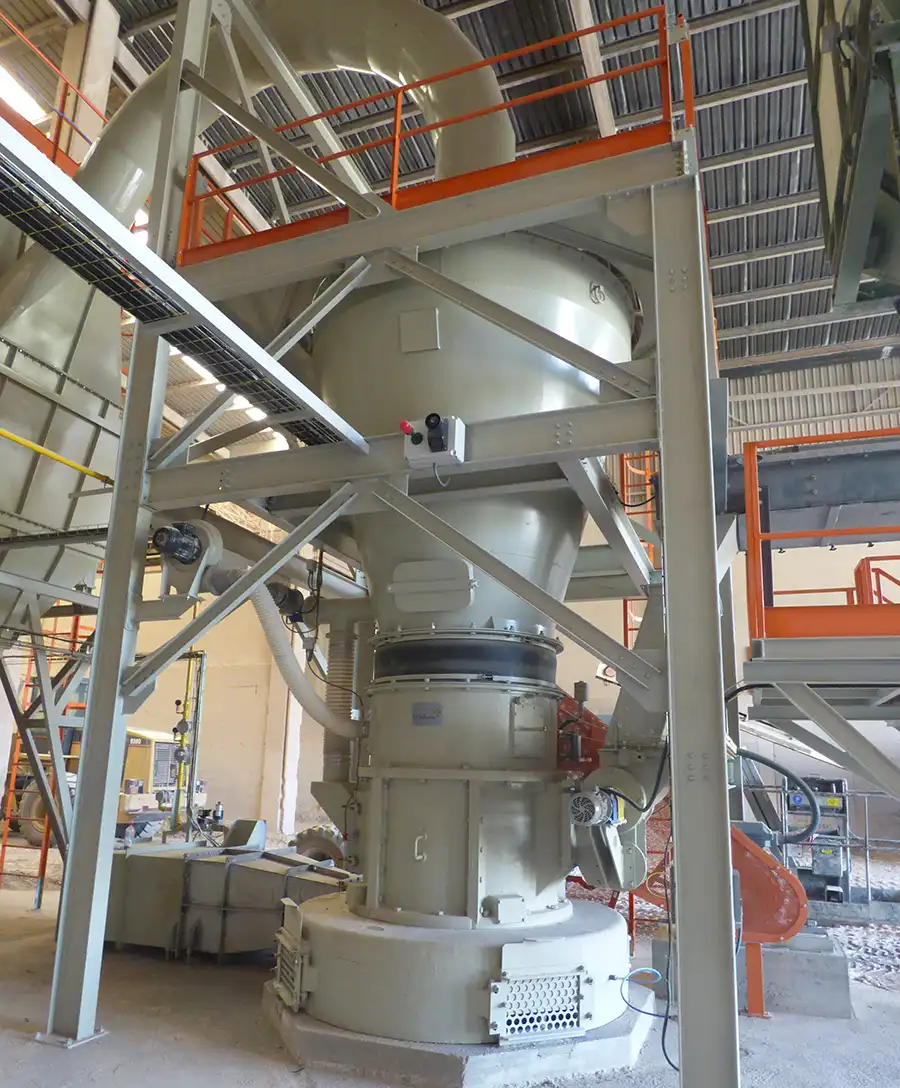
Molienda vía seca
Es un proceso utilizado en la industria para reducir el tamaño de partícula de materiales sólidos sin utilizar ningún tipo de líquido. En este proceso, los materiales sólidos se trituran y pulverizan mediante la acción mecánica de molinos, como molinos de bolas, molinos de martillos, molinos de rodillos, entre otros.
Su utilización en la industria es frecuente, debido a que es un proceso eficiente y económico para reducir el tamaño de partícula de una amplia variedad de materiales, como minerales, productos químicos, alimentos, entre otros.
El material se alimenta al molino y se tritura mediante la acción de impacto, corte y fricción entre las partículas y las superficies del molino. El material molido se recoge en un recipiente o silo, donde se puede almacenar para su posterior uso o procesamiento.
Este proceso tiene algunas ventajas en comparación con la molienda vía húmeda, como la menor necesidad de secado y la menor cantidad de residuos líquidos generados. Sin embargo, la molienda vía seca puede generar una mayor cantidad de polvo, lo que puede requerir medidas de seguridad adicionales para prevenir la exposición de los trabajadores a sustancias peligrosas.
En resumen, la molienda vía seca es un proceso utilizado en la industria para reducir el tamaño de partícula de materiales sólidos mediante la acción mecánica de molinos, y es un proceso eficiente y económico para una amplia variedad de materiales.
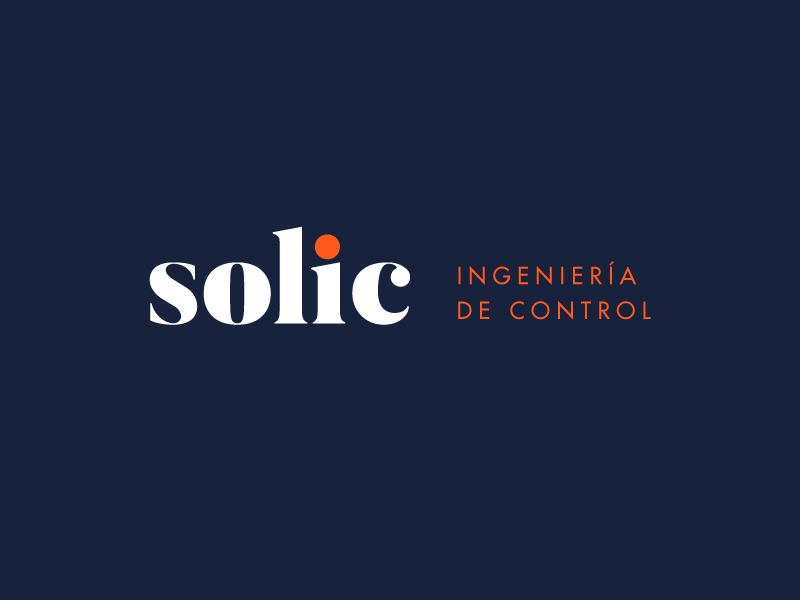
Sistema Control de producción (ICS)
Este tipo de sistemas pueden llevar desde unos pocos controladores modulares montados en panel hasta grandes sistemas de control distribuidos interactivos e interconectados con muchos miles de conexiones de campo. Todos los sistemas reciben datos recibidos de sensores remotos que miden las variables del proceso (PV), los comparan con los puntos de ajuste deseados (SP) y derivan funciones de comando que se utilizan para controlar un proceso a través de los elementos de control finales (FCE), como las válvulas de control.
Se Implementan mediante sistemas de control de supervisión y adquisición de datos (SCADA), o sistemas de control distribuido (DCS) y controladores lógicos programables (PLC).
Secado de arcillas
Es un proceso utilizado en la industria cerámica para reducir el contenido de humedad de las arcillas antes de su uso en la producción de objetos de cerámica. El secado de arcillas es una etapa importante en el proceso de producción de cerámica, ya que la humedad en las arcillas puede afectar negativamente la calidad y las propiedades finales del producto.
El mismo se realiza en cámaras de secado que se controlan cuidadosamente para mantener una temperatura y humedad adecuadas para el proceso de secado. Las arcillas húmedas se extienden en capas uniformes en estantes o bandejas, y se colocan en la cámara de secado. El aire caliente y seco se hace circular a través de las bandejas para acelerar el proceso de secado.
El tiempo de secado varía según el tipo de arcilla y la cantidad de humedad presente en ella, pero generalmente dura entre unas pocas horas y varios días. El proceso de secado de arcillas es crítico, ya que si se secan demasiado rápido, pueden agrietarse o deformarse, mientras que si se secan demasiado lentamente, pueden crecer moho o bacterias.
Una vez que las arcillas están completamente secas, se pueden moldear y dar forma para crear productos de cerámica como platos, tazas, jarrones, entre otros. El proceso de secado es una parte importante del proceso de producción de cerámica, ya que afecta directamente la calidad y las propiedades finales del producto.
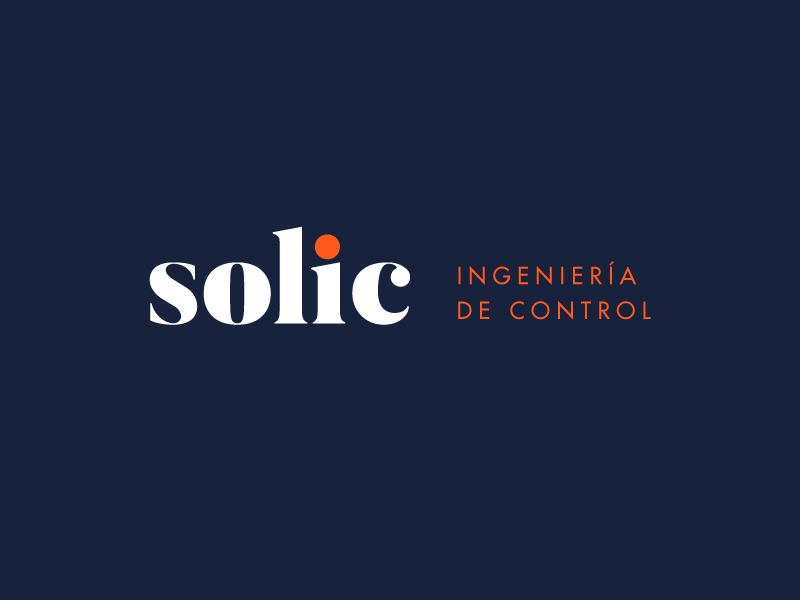
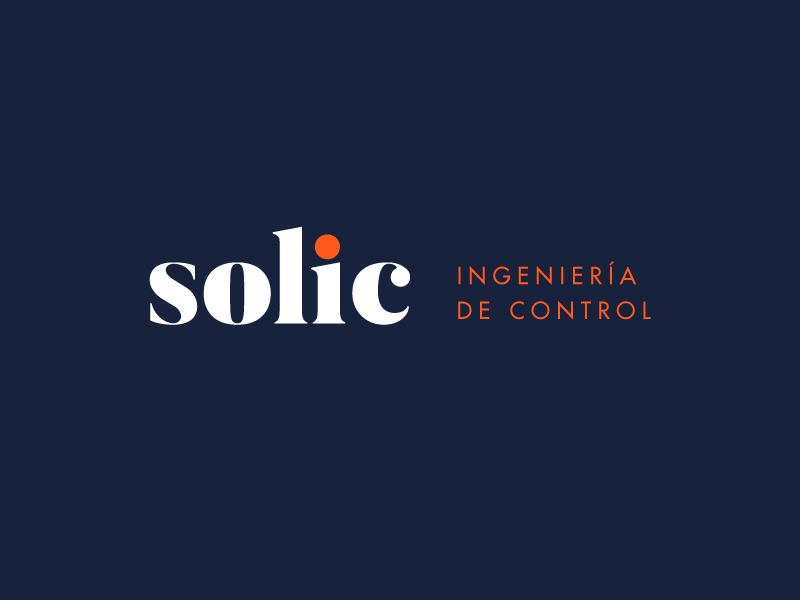
Secado de arcillas
Es un proceso utilizado en la industria cerámica para reducir el contenido de humedad de las arcillas antes de su uso en la producción de objetos de cerámica. El secado de arcillas es una etapa importante en el proceso de producción de cerámica, ya que la humedad en las arcillas puede afectar negativamente la calidad y las propiedades finales del producto.
El mismo se realiza en cámaras de secado que se controlan cuidadosamente para mantener una temperatura y humedad adecuadas para el proceso de secado. Las arcillas húmedas se extienden en capas uniformes en estantes o bandejas, y se colocan en la cámara de secado. El aire caliente y seco se hace circular a través de las bandejas para acelerar el proceso de secado.
El tiempo de secado varía según el tipo de arcilla y la cantidad de humedad presente en ella, pero generalmente dura entre unas pocas horas y varios días. El proceso de secado de arcillas es crítico, ya que si se secan demasiado rápido, pueden agrietarse o deformarse, mientras que si se secan demasiado lentamente, pueden crecer moho o bacterias.
Una vez que las arcillas están completamente secas, se pueden moldear y dar forma para crear productos de cerámica como platos, tazas, jarrones, entre otros. El proceso de secado es una parte importante del proceso de producción de cerámica, ya que afecta directamente la calidad y las propiedades finales del producto.
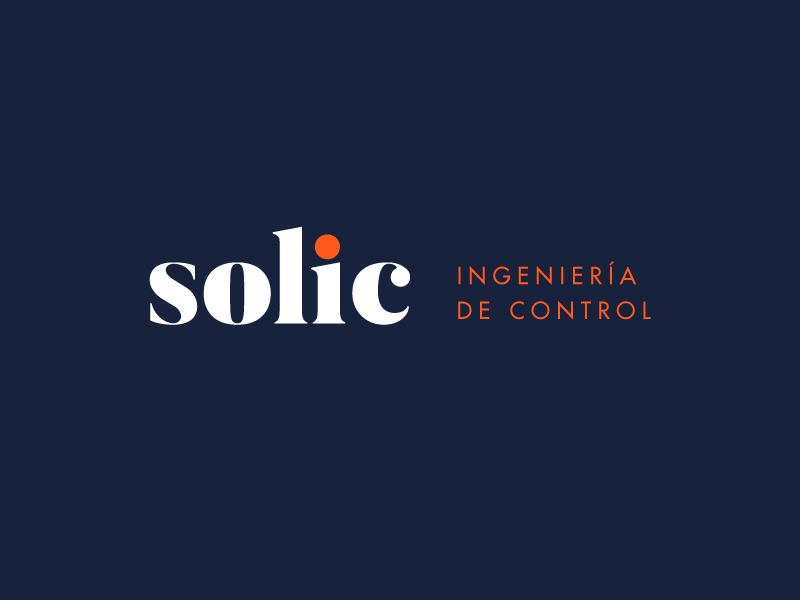
Cribado o Tamizado de arcillas (ICS)
Es un proceso en el que se separan las partículas de arcilla de diferentes tamaños utilizando una malla o tamiz. La arcilla se coloca en la parte superior del tamiz y se agita o se hace pasar a través de él, lo que permite que las partículas más pequeñas pasen a través de la malla mientras que las partículas más grandes quedan atrapadas en la superficie del tamiz.
Este proceso es comúnmente utilizado en la industria de la cerámica para eliminar las impurezas y asegurar que la arcilla tenga una textura uniforme y adecuada para su uso en la producción de baldosas cerámicas. También, puede ser utilizado en otras industrias que utilizan arcilla, como la construcción o la agricultura, para separar diferentes tamaños de partículas y mejorar la calidad del producto final.
Filtrado aire-medioambiente
El filtrado de aire en el medio ambiente se refiere al proceso de eliminar partículas y contaminantes del aire a través de la utilización de sistemas de filtración. Estos sistemas de filtración pueden ser instalados en una amplia variedad de entornos, como en las plantas de fabricación, edificios comerciales y residenciales, vehículos y sistemas de ventilación.
Los filtros de aire utilizados en el medio ambiente pueden ser de diferentes tipos, tales como filtros de fibra de vidrio, filtros de carbón activado, filtros electrostáticos y filtros HEPA (de alta eficiencia). Cada tipo de filtro es capaz de eliminar diferentes tipos de contaminantes del aire, incluyendo partículas, gases, olores y microorganismos.
Dicho filtrado es importante para la salud y seguridad de las personas, así como para la protección del medio ambiente en general. La calidad del aire puede ser afectada por una amplia variedad de factores, tales como la contaminación del tráfico, las emisiones industriales, y las emisiones de los hogares. El filtrado de aire ayuda a reducir la cantidad de contaminantes presentes en el aire y a mejorar la calidad del aire que respiramos.
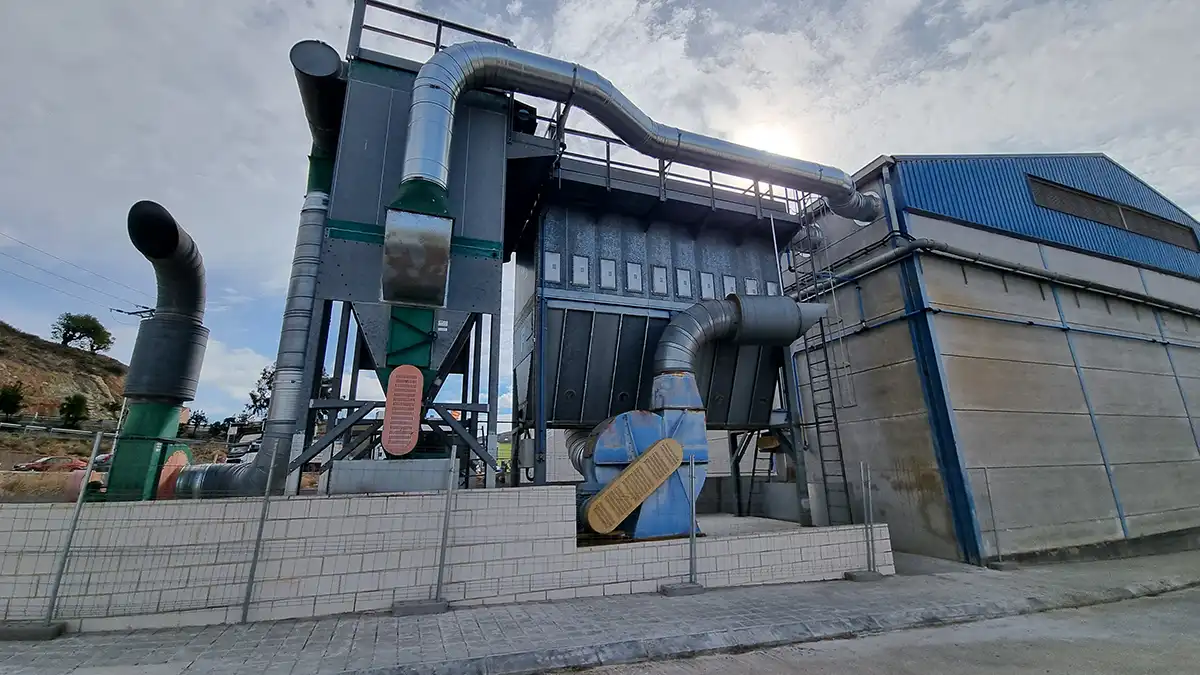
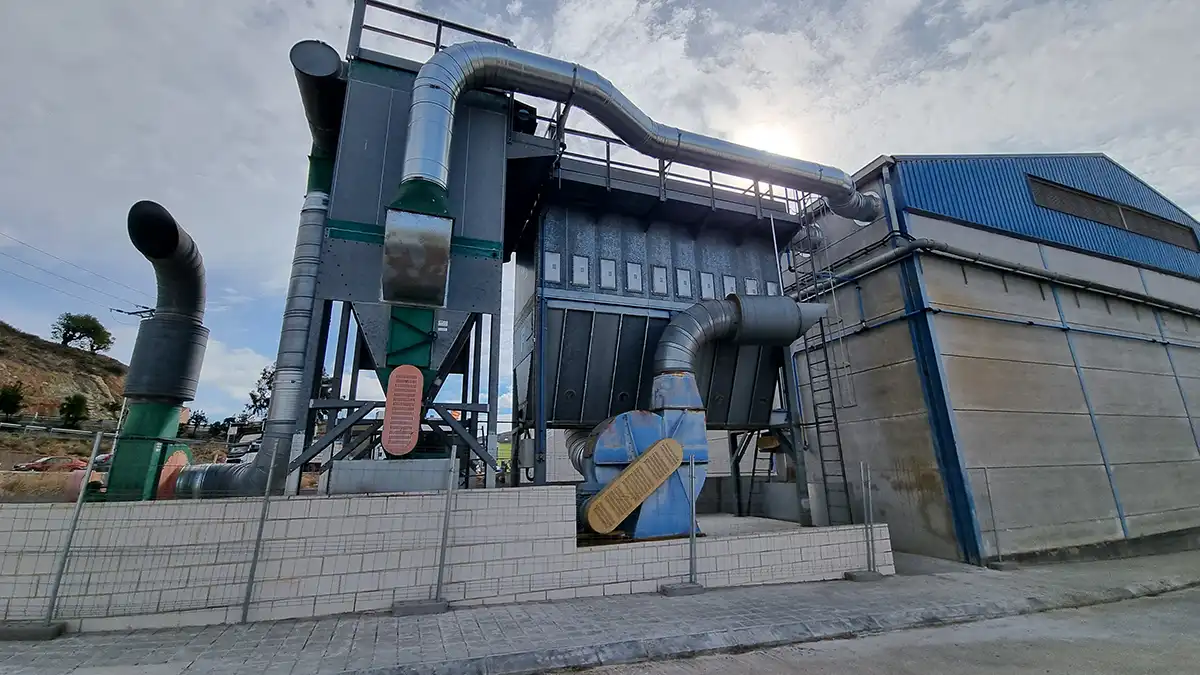
Filtrado aire-medioambiente
El filtrado de aire en el medio ambiente se refiere al proceso de eliminar partículas y contaminantes del aire a través de la utilización de sistemas de filtración. Estos sistemas de filtración pueden ser instalados en una amplia variedad de entornos, como en las plantas de fabricación, edificios comerciales y residenciales, vehículos y sistemas de ventilación.
Los filtros de aire utilizados en el medio ambiente pueden ser de diferentes tipos, tales como filtros de fibra de vidrio, filtros de carbón activado, filtros electrostáticos y filtros HEPA (de alta eficiencia). Cada tipo de filtro es capaz de eliminar diferentes tipos de contaminantes del aire, incluyendo partículas, gases, olores y microorganismos.
Dicho filtrado es importante para la salud y seguridad de las personas, así como para la protección del medio ambiente en general. La calidad del aire puede ser afectada por una amplia variedad de factores, tales como la contaminación del tráfico, las emisiones industriales, y las emisiones de los hogares. El filtrado de aire ayuda a reducir la cantidad de contaminantes presentes en el aire y a mejorar la calidad del aire que respiramos.
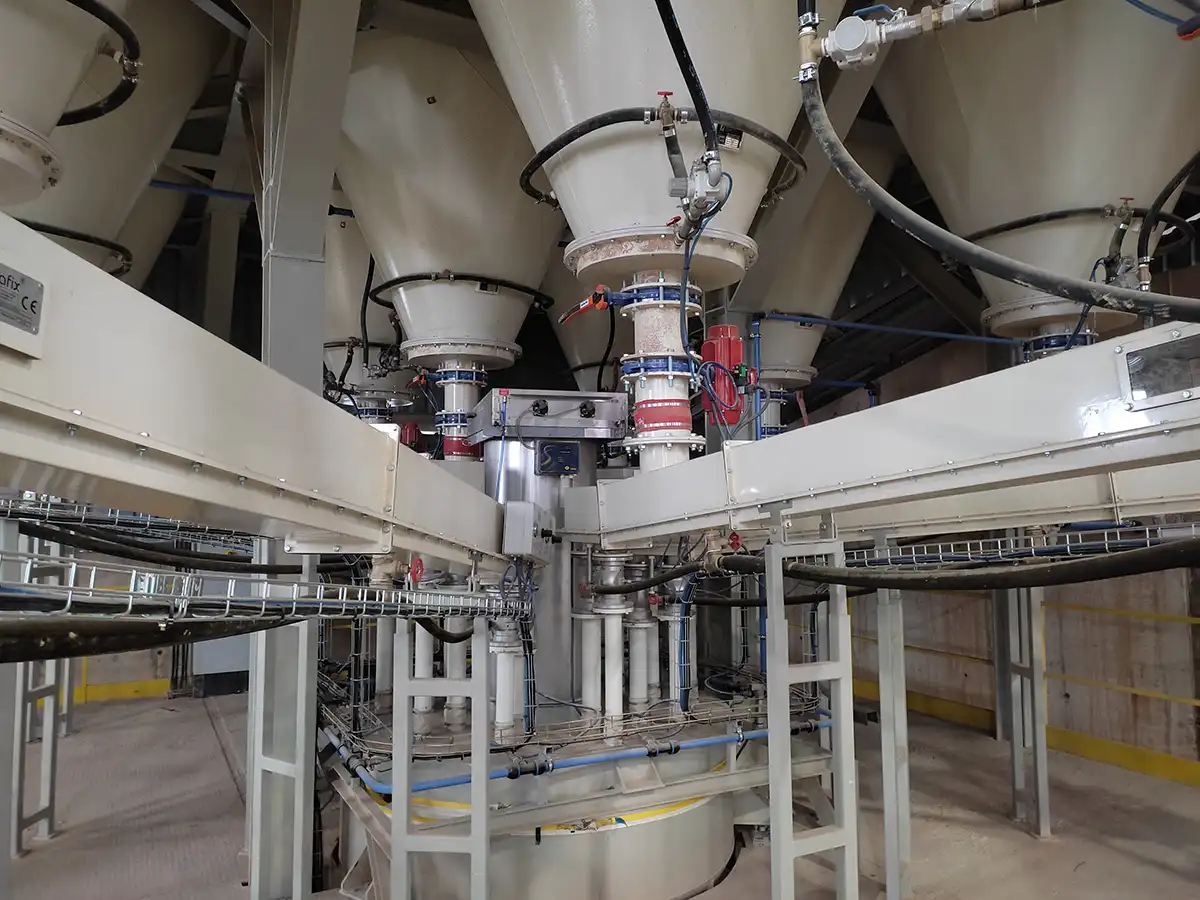
Dosificación por batch o BIG BAG
Dosificación por batch o BIG BAG
Se refiere a un proceso automatizado utilizado en la industria para medir y mezclar ingredientes en cantidades específicas para la producción de productos. Esta técnica implica el uso de contenedores o bolsas de gran tamaño (BIG BAG) que contienen los ingredientes a dosificar, y una aplicación informática WEB que controla la receta, las órdenes de producción, el stock y los consumos.
El proceso es muy preciso, con un margen de error inferior al 1%, lo que garantiza una alta calidad y uniformidad del producto final. Además, el sistema cuenta con una trazabilidad completa de los ingredientes utilizados, lo que significa que se puede rastrear todo el proceso de producción desde el inicio hasta el final. Esta trazabilidad permite una mayor eficiencia en la producción y la capacidad de detectar y corregir errores o problemas en tiempo real.
También se considera una técnica de la INDUSTRIA 4.0, que utiliza tecnologías de la información y la comunicación para crear procesos de producción más eficientes y automatizados. Esto significa que el sistema puede adaptarse a diferentes requisitos de producción, como cambios en la receta o en la cantidad de producto producido, y que puede ser monitoreado y controlado de forma remota.
Dosificación por depeso
Es un proceso de medición de materiales en la producción industrial que utiliza una báscula o balanza para medir la cantidad precisa de un material a utilizar en una receta o mezcla. En este proceso, se pesa el material en una báscula y se controla la cantidad de material dispensado mediante un sistema de control electrónico.
Además, es un método preciso y confiable para medir la cantidad exacta de materiales que se necesitan para una producción determinada. Este método es especialmente útil en la producción de alimentos, productos farmacéuticos, químicos y otros productos que requieren una medición precisa de los ingredientes.
Este proceso de dosificación puede ser totalmente automatizado con el uso de sistemas de control electrónico, lo que permite un mayor control y eficiencia en la producción. Igualmente, dicho proceso por peso es rápido y eficiente, lo que resulta en una mayor productividad y una reducción en los costos de producción.
Dosificación por cinta transportadora
Es un proceso utilizado en la industria para medir y controlar la cantidad de material que se mueve a lo largo de una cinta transportadora. En este proceso, el material se coloca en la cinta transportadora, que se mueve a una velocidad determinada para medir la cantidad de material que se dosifica.
Especialmente útil en la producción de materiales a granel, como la arena, el cemento, los agregados y los productos químicos. Este proceso se utiliza para controlar la cantidad exacta de material que se mueve a lo largo de la cinta transportadora, lo que garantiza una medición precisa y uniforme del material.
De igual modo, se puede controlar mediante un sistema de control electrónico que ajusta la velocidad de la cinta transportadora para garantizar la cantidad correcta de material dosificado. Este proceso es muy preciso y permite una dosificación constante y uniforme del material, lo que mejora la calidad del producto final.
Además, es un proceso altamente eficiente, ya que permite la dosificación de grandes cantidades de material en poco tiempo. También es un proceso muy seguro, ya que la cinta transportadora está diseñada para evitar el desbordamiento y la caída de materiales, lo que reduce el riesgo de lesiones y accidentes en el lugar de trabajo.
En resumen, la dosificación por cinta transportadora es un proceso utilizado en la producción industrial para dosificar y medir de manera precisa y uniforme la cantidad de materiales a granel, lo que mejora la calidad del producto final y aumenta la eficiencia de la producción